![]() |
What is a Multiple Hearth Furnace?
Most people have never heard of a Multiple Hearth Furnace. Some people may refer to a Multiple Hearth Furnace as a “Multiple Hearth Incinerator,” a “Multiple Hearth Roaster,” “Retort Furnace,” “MHF,” or “MHI,” “Calciner,” among a myriad of similar or more specific names.
Definition of a Multiple Hearth Furnace
A multiple hearth furnace is a furnace consisting of several round, stacked hearths. The hearths are basically floors within a large cylinder. The hearths alternate between in-hearths and out-hearths. In-hearths have a large hole in the center, for material to pass through to the hearth below. Out-hearths, have holes around the perimeter of the hearth for material to pass through to the hearth below.
A Multiple Hearth Furnace is usually employed when a large volume of material needs to be thermally processed, provided that the material is:
- Moderately uniform in content
- Steady, continuous feed
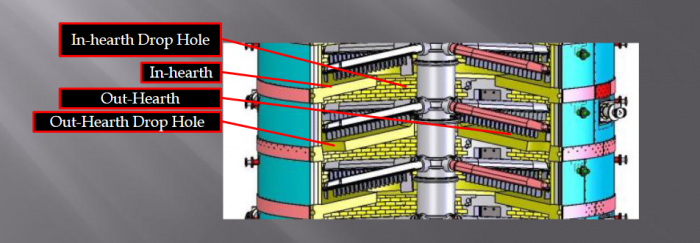
Benefits of a Multiple Hearth Furnace
Multiple Hearths = Multiple Zones
- The material can go through separate stages, such as drying, devolatilizing, calcining, reduction, oxidization...
- With careful control, and proper I&C each zone can be closely monitored and the proper atmosphere can be maintained in each zone.
Production Rates and Quality
- Because the process can be so closely monitored, maximum production and quality rates can be achieved.
Energy Usage
- Many processes can be run autogenously; reducing or eliminating fuel usage.
- Relatively low horsepower requirements for fans and centershaft.
Turn Down
- While an MHF “prefers” constant feed. Many processes allow for a wide turn-down ratio without loss of efficiency. Some competing technologies suffer greatly when product feed does not meet the design criteria.
Reduced Floor Space Requirement
- Because the hearths are stacked, a larger furnace can be installed in less space. A choice of diameters can make the space savings significant. Some of our competition requires significantly more floor space to approach the capacity easily achieved with an MHF.
- MHFs can be raised on legs to accommodate material handling equipment underneath the furnace, such as ash handling equipment, or even discharging directly into another process furnace.
Low Maintenance Requirements
- Multiple Hearth Furnaces are designed and built to be run year round with minimal internal maintenance, meaning fewer shut-downs. Some customers even mortar the doors shut because they hardly ever need to open them.
- The fans and motors are generally smaller, requiring less maintenance.
Construction of a Multiple Hearth Furnace
- Multiple Hearth Furnaces generally utilize a steel shell, with refractory lining.
- Skew Bands are used to support the hearths, and appear as rings on the outside of the shell.
- The refractory lining and hearths are generally made of bricks. The hearths are self supporting three dimensional sprung arches, and distribute all of their weight to the shell and skew band.
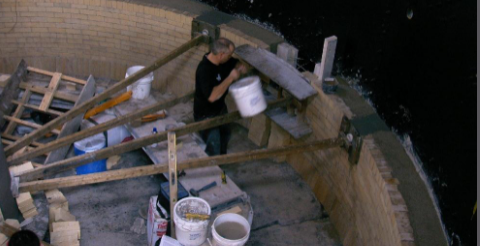
Material Movement in a Multiple Hearth Furnace
Material is fed into the top of the furnace, and is moved down, from hearth to hearth, until it exits at the bottom.
Centershaft, Rabble Arms, Rabble Teeth
- The Centershaft is a vertical shaft through the furnace. It spins slowly. This turning swings the “Rabble Arms” which are holding “Rabble Teeth.”
- The Rabble Teeth plow the material across the hearths toward the drop holes.
- This rabbling action, stirs the material and exposes new material to the furnace atmosphere.
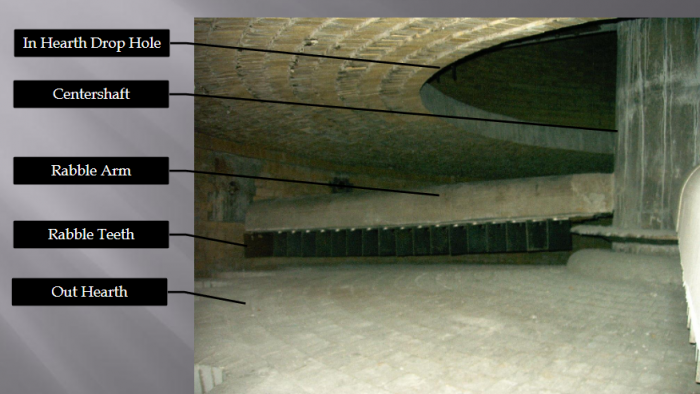
Multiple Hearth Furnace Thermal System
- The Multiple Hearth Furnace can be operated at a wide range of temperatures. The hearths allow for zoning of the atmospheres, including temperatures.
- The energy to meet the desired temperature can come from the chemical process of the material, or from burners. Hearths can even be artificially cooled using air, mist, or steam injection.
- Multiple Hearth Furnaces use burners to heat the furnace, and dry-out the refractory before feed is initiated. Then burners are used to maintain temperatures as needed.
- The burners can burn any fuel. Most common are fossil fuels (Natural Gas, Propane, Oil) but other fuel sources are possible.
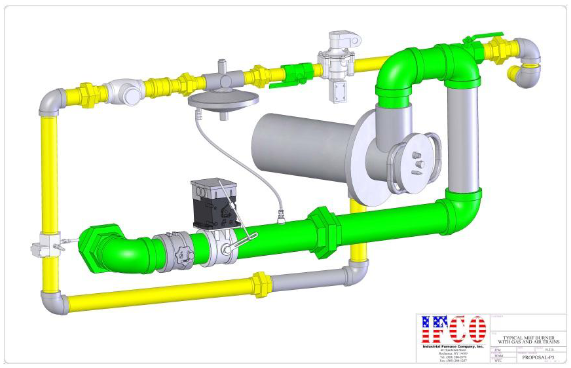
Multiple Hearth Furnace Instrumentation and Controls
- Multiple Hearth Furnaces can be built, or rebuilt with state-of-the-art control systems. Advanced Process Controls can be used to optimize the system for maximum product yield, product quality, and fuel savings.
- Control packages can be customized to give the customer a fully automated machine, to a basic package that requires manual intervention at every step.
- All systems can be automated. The most common automation is the temperature, which is usually controlled by the burners.
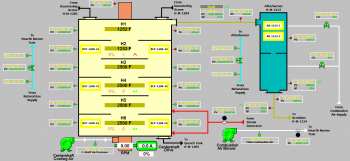